CALCESTRUZZO LEGGERO STRUTTURALE AUTOCOMPATTANTE (LS-SCC) PRODOTTO CON ARGILLA
Postato il di edilweb
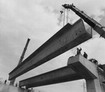
INTRODUZIONE
Il calcestruzzo leggero strutturale è apparso sul mercato dei materiali per
edilizia negli anni ’70 seguendo lo sviluppo tecnologico e produttivo
dell’argilla espansa che, come noto, è un materiale espanso ottenuto dalla
cottura di argille naturali all’interno di grandi forni rotanti a temperature
superiori a 1000°C.
Ciò che caratterizza questo materiale, impiegabile come aggregato nei
calcestruzzi, è la buona costanza qualitativa frutto dell’attenta selezione
delle materie prime e del rigido controllo del processo di produzione.
I vantaggi di produrre un calcestruzzo leggero strutturale a densità 1600-1900
kg/mc rispetto ad uno ordinario sono numerosi, sia dal punto di vista
ingegneristico che ambientale (1, 2).
Assai più recente invece è la comparsa del calcestruzzo autocompattante. Tale
prodotto è caratterizzato da prestazioni, in termini di lavorabilità,
eccezionali per non dire assolute poiché non richiede lavoro o energia per la
sua messa in opera, ma ha prerogative intrinseche di autocompattazione e
capacità di riempimento dei casseri sfruttando il solo peso proprio. La qualità
dell’SCC dipende principalmente da un corretto dosaggio delle polveri
comprensive di cemento, aggiunte minerali e passante a 0.125 mm proveniente
dalle sabbie. Di conseguenza, quando il contributo di queste ultime è
quantitativamente rilevante (es. sabbie di frantumazione, ormai sempre più
frequenti), una loro variazione granulometrica può compromettere profondamente
la robustezza e la stabilità degli impasti allo stato fresco.
Da Enco Journal n. 47 - 2009
Recentemente sono stati fatti diversi studi inerenti la combinazione di queste
due tecnologie (6,7). Caratteristica comune di tutte queste sperimentazioni, è
la presenza nel mix-design di questi calcestruzzi di un quantitativo rilevante
di sabbia fine naturale.
La sabbia naturale è tipicamente aggiunta nel calcestruzzo leggero strutturale
per controllarne la densità, ottenere elevate resistenze meccaniche e per
compensare la scarsità di parti fini che tipicamente caratterizza l’argilla
espansa.
Lo scopo della ricerca sperimentale oggetto della presente pubblicazione, è
analizzare la possibilità di produrre un calcestruzzo leggero strutturale
autocompattante caratterizzato dalla totale assenza di aggregati naturali di
peso normale.
Una miscela di calcestruzzo autocompattante leggero senza sabbia naturale ha tre
vantaggi principali: riduzione della variabilità della lavorabilità dovuta alle
inevitabili oscillazioni nel contenuto di finissimi nella sabbia, specialmente
se di frantumazione; soluzione al problema della diminuzione di disponibilità di
sabbia naturale; incremento del rapporto resistenza/densità.
Il principale problema di questo tipo particolare di miscela, è quello di
conferire la giusta coesione e scorrevolezza all’impasto evitando nel contempo
il fenomeno della segregazione inversa dell’argilla espansa.
Esiste infatti una intrinseca caratteristica negativa nel concetto di SCC, messa
formalmente in evidenza dalla relazione di Stokes (in base alla quale la
velocità finale Vs di una particella in un mezzo fluido è direttamente
proporzionale alla differenza di densità tra particella e fluido, direttamente
proporzionale alla dimensione della particella e inversamente proporzionale alla
viscosità del fluido), che riguarda la sensibile differenza di densità tra la
pasta (normalmente il suo valore è intorno a 1.90-2.10 kg/l) e gli aggregati
grossi (di densità 2.60-2.75 kg/l nel caso questi siano comuni e 1.25-1.67 kg/l
nel caso siano argille espanse strutturali). Ciò fa si che, se la viscosità
della pasta legante a basse velocità di deformazione non ha valori ottimali,
l’aggregato può sedimentare o galleggiare tanto più velocemente quanto più
grandi sono le sue dimensioni (segregazione statica).
Fondamentale per la realizzazione di tale prodotto è quindi l’impiego di una
particolare tipologia di argilla strutturale caratterizzata da elevate
prestazioni meccaniche e Dmax di
soli 8 mm, unitamente ad una speciale combinazione di additivi chimici.
Quest’ultima è composta da un agente aerante, un viscosizzante e un
superfluidificante acrilico in grado di produrre una modificazione delle
caratteristiche fisiche della pasta legante consistenti in una riduzione della
sua densità, attraverso l’introduzione di un sistema stabilizzato di microbolle
d’aria e un aumento della sua viscosità.
MATERIALI E METODI
Durante la sperimentazione di laboratorio sono state confezionate diverse
miscele di prova utilizzando i seguenti materiali:
• Due diversi cementi CEM II/A-LL 42.5R denominati Cem A e Cem B, entrambi con
densità di 3.00 kg/l.
• Filler calcareo caratterizzato da un passante del 100% a 0.100 mm e una
densità di 2.70 kg/l.
• Argilla espansa strutturale sinterizzata 0.25/8 mm le cui caratteristiche sono
riportate in Tabella 1 e Figura 1.
• Superfluidificante acrilico con una densità di 1.1 kg/l.
• Stabilizzante in polvere composto da una miscela di aerante e viscosizzante
Al fine di avere un maggior controllo sulle proprietà del calcestruzzo,
l’argilla espansa è stata pre-bagnata per 24 ore prima del suo impiego (3).
Per la caratterizzazione delle proprietà allo stato fresco del calcestruzzo si
sono utilizzate le prove di Slump flow, V-funnel e L-box. Le ultime due sono
state impiegate per la valutazione della tendenza alla segregazione. Tutte
queste prove sono state condotte oltre che a tempo 0’ anche dopo 30’ e 60’ per
la valutazione del mantenimento della lavorabilità.
Le prove di resistenza meccanica a compressione sono state eseguite su provini
cubici lato 150 mm, stagionati a 20°C e U.R. > 95%, a 1, 7 e 28 giorni.
Le miscele sono state preparate impiegando una comune mescolatrice a bicchiere
da laboratorio seguendo la seguente procedura: introduzione dell’argilla espansa
saturata insieme al cemento, il filler e al 75% dell’acqua di impasto. Dopo 10
minuti di mescolazione introduzione degli additivi insieme alla restante acqua.
Mescolazione finale della durata di 5 minuti.
Al fine di simulare le reali condizioni di trasporto in autobetoniera, dopo la
prima valutazione della lavorabilità a tempo 0’, la miscela di calcestruzzo è
stata mantenuta in continua agitazione all’interno della mescolatrice a
bicchiere, appositamente modificata per tale scopo, ad una velocità di 3 giri al
minuto. Appena prima dell’esecuzione delle prove di lavorabilità a 30’ e 60’, la
miscela è stata mescolata ad alta velocità per 2 minuti.
RISULTATI E DISCUSSIONE
Una volta misurata la densità dell’argilla espansa in condizioni di
S.S.A. (1.6-1.65 kg/l), la composizione dell’agente stabilizzante
(aerante+viscosizzante) è stata ottimizzata al fine di conferire un’adeguata
viscosità alla pasta legante e ottenere una densità della stessa il più simile
possibile a quella dell’argilla saturata (minimizzazione della velocità
terminale Vs). Dopo diverse prove di laboratorio, si è trovato che una densità
della pasta legante compresa tra 1.74-1.83 kg/l è in grado di conferire buona
stabilità alla miscela allo stato fresco senza causare un eccessivo calo delle
resistenze meccaniche allo stato indurito.
In Tabella 2 sono mostrate le composizioni delle diverse miscele di calcestruzzo
testate. La quantità di acqua e additivi è rimasta costante in tutte le prove.
Dopo aver messo a punto la miscela utilizzando il Cem A (miscele A, B, C), si è
proceduto ad una sua verifica utilizzando il Cem B (miscela D). Quest’ultima
ricetta è stata infine utilizzata per eseguire una prova di riempimento di una
piccola cassaforma di legno in presenza di armatura metallica (miscela E).
Lavorabilità
In Tabella 3 e nelle Figura 2, 3 e 4 sono riportati i risultati delle
prove di filling ability (Slump flow, V-funnel), passing ability e resistenza
alla segregazione dinamica (L-box).
Come si vede, la miscela A mostra un ottimo comportamento a tempo 0’,
come indicato dai valori di Slump flow (780 mm) e V-funnel (6 s) oltre che dalla
totale assenza di segregazione, confermata dal valore di L-Box (0.89) e
dall’osservazione diretta. Dopo 60’ però, nonostante il buon valore di Slump
flow (670 mm), la prova all’L-Box è stata negativa (0.70) indicando un
peggioramento del passing ability. L’osservazione visiva ha confermato la
comparsa di un fenomeno di segregazione inversa. Al fine di risolvere tale
problema, il contenuto di cemento è stato aumentato da 420 kg/m3 nella
miscela A fino a 490 kg/m3 nella miscela C. A seguito di tale modifica la
lavorabilità è migliorata protraendosi per oltre 60’ senza alcun segno di
segregazione, come dimostrato dal superamento del test dell’L-Box (H2/H1= 0.8).
Tali risultati sono stati infine confermati impiegando un diverso cemento
(miscele D e E).
Al fine di simulare il comportamento di questo calcestruzzo in una reale
situazione di getto, con la miscela E è stata effettuata una prova di
riempimento di una cassaforma in legno di 2.5 m di lunghezza, 1.1 m di altezza,
10 cm di profondità in presenza di una armatura di rinforzo. Come mostrato nella
Figura 5, la prova ha avuto esito positivo non essendo visibile alcun segno di
segregazione o nidi di ghiaia.
Sviluppo di calore
A causa dell’elevata quantità di cemento presente e della bassa
conducibilità termica di questo tipo di calcestruzzo, lo sviluppo di calore
all’interno della suddetta cassaforma in legno è stato monitorato con una
termocoppia PT100 annegata all’interno del calcestruzzo (miscela E) ad una
profondità di 20 cm dalla superficie.
Come si può vedere nel grafico in Figura 6, la massima temperatura interna
raggiunta è stata di 44°C dopo 15 ore e 30 minuti dal getto. Il gradiente
massimo allo scassero è stato di circa 20°C, nonostante ciò, né al momento dello
scassero né successivamente, si sono rilevate fessurazioni di origine termica.
Quest’ultimo comportamento è probabilmente dovuto al più basso modulo elastico
di questo calcestruzzo rispetto ad un analogo calcestruzzo di peso normale (4,
7).
Resistenze meccaniche
In Tabella 4 e Figura 7 sono riassunti i risultati della resistenza
meccanica a compressione.
Come previsto l’impiego dell’argilla espansa e l’introduzione di un elevato
volume di microvuoti, ha comportato un abbassamento delle resistenze meccaniche
rispetto ad un calcestruzzo di peso normale di pari rapporto a/c. E’ noto
infatti che la resistenza a compressione di un calcestruzzo normale dipende
principalmente dal rapporto a/c, essendo la resistenza a compressione degli
aggregati lapidei generalmente superiore a 100 MPa.
Ad ogni modo grazie al basso rapporto a/c (0.38) e alle ottime proprietà
meccaniche dell’argilla espansa impiegata, avente Dmax =
8 mm, si sono raggiunte resistenze meccaniche a compressione fino a 55 MPa a 28
gg.
Ritiro igrometrico
Il ritiro igrometrico è stato valutato a 60 giorni su provini 10 cm x 10
cm x 50 cm stagionati alle condizioni di 20°C e U.R. 50%, come indicato dalla
normativa italiana UNI 6555. Così come per le resistenze meccaniche, il basso
rapporto a/c e le ottime proprietà meccaniche dell’argilla, hanno permesso di
ottenere un valore dello stesso di soli 550 µm/m, cioè comparabile al ritiro di
un calcestruzzo autocompattante “ordinario” di analogo contenuto di polveri e
pari resistenza meccanica.
Prova di pompabilità
Al fine di confermare i dati ottenuti nella sperimentazione di
laboratorio e verificare la pompabilità di questo calcestruzzo, è stata eseguita
una prova industriale presso un impianto di betonaggio. La prova è stata
condotta su sei metri cubi di calcestruzzo miscelato a secco in autobetoniera.
L’argilla è stata caricata in botte la sera precedente insieme a 1000 lt di
acqua per la preventiva saturazione. Il giorno seguente, in fase di carico si è
proceduto all’aggiunta del cemento, del filler e infine dell’additivo.
La prova in autobetoniera ha rivelato una certa difficoltà nella miscelazione
come evidenziato dall’abbondante presenza di agglomerati sferici del diametro di
circa 15-20 cm, costituiti in larga misura da materiale fine. Il prolungamento
del tempo di miscelazione finale non ha comportato alcun miglioramento.
Il calcestruzzo ha mostrato elevata scorrevolezza (slump flow 760 mm) sebbene
rispetto alle precedenti esperienze di laboratorio sia apparso un po’ più “magro”
e viscoso. Nonostante tali differenze tra laboratorio e cantiere, la prova di
pompabilità è stata positiva; il materiale è stato pompato senza interruzioni
all’interno di un ampio scavo evidenziando le sue caratteristiche autolivellanti.
Lo sforzo della pompa è stato il medesimo che per un “comune” calcestruzzo
autocompattante.
CONCLUSIONI
In questo studio è stato dimostrato come sia possibile produrre un
calcestruzzo leggero strutturale autocompattante, definito LS-SCC (lightweight
structural self-consolidating concrete), altamente performante sia allo stato
fresco che a quello indurito, facendo riscorso alla sola argilla espansa come
aggregato, senza cioè alcuna aggiunta di sabbia naturale.
Le ottime proprietà meccaniche dell’argilla espansa utilizzata (Dmax=
8 mm), unitamente al basso rapporto a/c, hanno permesso la produzione di miscele
di calcestruzzo leggero con resistenze meccaniche fino a 55 MPa a 28 giorni e
densità allo scassero di 1700 ± 50 kg/m3. Il ritiro igrometrico
misurato a 60 giorni è stato modesto, 550 µm/m, cioè del tutto paragonabile al
ritiro di un calcestruzzo autocompattante “ordinario” di analogo contenuto di
polveri e pari resistenza meccanica.
Per assicurare l’ottima lavorabilità sia in termini di filling ability (Slump
flow fino a 800 mm), che di passing abiliy (H2/H1 ≈ 1 all’L-Box) è stato
necessario l’impiego di un quantitativo di finissimi pari a 730 kg/m3 unitamente
all’aggiunta di un sistema di additivi composto da una superfluidificante
acrilico, un agente aerante ed un agente viscosizzante. Il mantenimento della
lavorabilità è stato molto buono tanto che le proprietà autocompattanti sono
perdurate per oltre 1 ora.
Prove industriali hanno indicato una certa difficoltà di omogeneizzazione della
miscela allorquando venga utilizzata la procedura di mescolazione a secco dei
componenti descritta nell’articolo. A tal proposito si ritiene che tale
problematica possa essere agevolmente risolta impiegando una produzione ad umido
(premescolatore) o una miscelazione mediante il sistema brevettato “C.H.T.T.” (premescolazione
della pasta legante additivata e successiva miscelazione con gli aggregati) (8).
In ogni caso è intenzione degli autori verificare se, pur adottando una
mescolazione a secco, l’utilizzo di una diversa procedura di carico (ordine di
aggiunta dei componenti, tempi di mescolazione, ecc.) possa limitare al massimo
tale problematica.
Con i dovuti accorgimenti di cui sopra, è ragionevole pensare che l’assenza
della sabbia naturale, inevitabilmente soggetta a variazioni granulometriche
specialmente nel suo contenuto di parti finissime, e l’utilizzo di soli prodotti
“industriali” soggetti a rigidi controlli di produzione, contribuiscano a
rendere la produzione di questo tipo di calcestruzzo più costante ed efficiente
(5). Questo nuovo concetto di calcestruzzo leggero strutturale inoltre, seppur
nella sua specificità, contribuisce ad uno sviluppo sostenibile in virtù delle
sue caratteristiche termo-isolanti e del mancato sfruttamento delle sempre meno
disponibili cave di sabbia naturale (6).
A tal riguardo sono in programma ulteriori studi per analizzare la possibilità
di una riduzione dei costi di produzione sostituendo una significativa quantità
di cemento con altri leganti come: loppa d’altoforno, cenere volante, ecc.
Questo aspetto, insieme alla valutazione di altre proprietà meccaniche come
modulo elastico, resistenze a flessione, creep, saranno oggetto di ulteriori
indagini.
RINGRAZIAMENTI
Si ringraziano le aziende Laterlite s.p.a e Unical s.p.a per il loro
contributo alla realizzazione delle prove su campo.
BIBLIOGRAFIA
1. Moira, A., “ Structural lightweight aggregate concrete”; Concrete
Construction, July 1995
2. NRMCA, “Structural lightweight concrete”; Concrete in Practice, 2003
3. Coppola, L., Monosi, S., Collepardi, M., “Il calcestruzzo leggero”; Nuovo
cantiere, October 1995
4. ACI Committee 213, “Guide for structural lightweight aggregate concrete”;
American concrete institute, 1967
5. ACI Committee 304, “Batching, mixing and job control of lightweight
concrete”; American Concrete Institute, 1991
6. Schuitemaker, E.J., van Breugel, K., den Uijl, J.A., “Design of
self-compacting lightweight concrete with environment-friendly lightweight
aggregate”; proceedings of the 3rd International Symposium on Self-Compacting
Concrete, Reykjavik, Iceland, August 2003
7. Collepardi, M., Borsoi, A., Collepardi, S., Troli, R., “Recent developments
of special self-compacting concretes”; proceedings of the 7th International
CANMET/ACI Conference on recent advances in concrete technology, Las Vegas, USA,
May 2004
8. Cadore, R., Capecchi, C., Bianchin, G., Campinoti, C., “La premescolazione
della pasta di cemento”; inConcreto 66, 2005.
|
|
| |
 |
 |
Votazione Articolo
|
 |
|
 |
 |
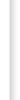 |
|
Risultato medio: 5 Voti: 1

|
|
 |
 |
 |
 |
 |
 |
 |
|