Lo scopo di questo lavoro è di valutare se le
ceneri provenienti dalla combustione di fanghi
di cartiera possano essere utilmente
reimpiegabili in qualità di aggiunte minerali
per la produzione di calcestruzzi
autocompattanti, ponendo l’attenzione sia alle
proprietà reologiche dello stato fresco sia alle
prestazioni meccaniche e al comportamento
deformativo da essiccamento dello stato indurito
[Collepardi et al, 2005; Bonen e Shah, 2005].
I fanghi di cartiera sono sottoprodotti della
produzione della carta. Circa 6 kg di fango
vengono prodotti per ogni tonnellata di carta.
Nel 2004, la produzione italiana complessiva di
fanghi di cartiera fu di circa 6•105 tonnellate
[Asquini et al, 2008].
I fanghi di cartiera sono composti da filler
minerali, sali inorganici, piccole fibre di
cellulosa, acqua e composti organici. La
composizione dei filler minerali dipende dal
tipo di carta prodotta. I fanghi di cartiera
vengono spesso inceneriti nelle cartiere stesse
per ridurne il volume da smaltire in discarica
e, a volte, per produrre energia per usi interni
bruciando i fanghi assieme a residui di legno.
Questo processo viene ottenuto mediante
disidratazione a basse temperature (< 200°C),
seguita da incenerimento ad elevate temperature
(> 800 °C). Durante l’incenerimento, carta e
componenti organiche vengono bruciati a
temperature comprese nell’intervallo 350÷500°C,
mentre i filler minerali ed i sali inorganici
vengono trasformati nei rispettivi ossidi a
temperature più elevate (> 800°C). CaO, Al2O3,
MgO e SiO2 sono gli ossidi più abbondantemente
presenti nei fanghi di cartiera inceneriti [Liaw
et al, 1998]. I fumi di combustione trasportano
le particelle leggere di cenere volante che in
tal modo possono essere intercettate e raccolte
per impiegarle come sottoprodotto riciclabile.
Se non riciclate tali ceneri andrebbero
conferite in discarica a costi elevati in quanto
catalogate come rifiuto speciale (pur se non
pericoloso). Il loro reimpiego avrebbe quindi
una duplice valenza ambientale ed economica.
Alcuni tentativi di riutilizzo di tali ceneri
sono rintracciabili in letteratura [Marcis et
al, 2005; Ernstbrunner 2007; Liaw et al, 1998],
in cui le ceneri di cartiera sono state
miscelate con altri ingredienti per la
produzione di cementi di miscela o mattoni.
Infatti i principali elementi costituenti le
ceneri da cartiera sono Al, Mg, Si e Ca, i cui
ossidi vengono largamente impiegati
nell’industria ceramica.
MATERIALI IMPIEGATI
In qualità di legante è stato impiegato un
cemento portland di miscela al calcare CEM
II/A-L 42.5 R secondo EN-197/1; quindi, per
realizzare una miscela di riferimento sono stati
impiegati i seguenti costituenti solidi: una
sabbia silicea (0-4 mm), un ghiaietto di
frantumazione (5-15 mm) ed un filler calcareo
(L, dall’inglese ‘limestone’) con finezza Blaine
pari a 0.52 m2/g.
In alternativa al filler calcareo, in questa
sperimentazione sono state preparate delle
miscele contenenti ceneri di combustione dei
fanghi di cartiera (PMA, acronimo dall’inglese
‘Paper Mill Ash’). Tali ceneri sono state
impiegate al posto del filler calcareo secondo
due modalità: ceneri tal quali (PMAtq) così come
prodotte in cartiera (Fig. 1), oppure dopo
macinazione (PMAmac), finalizzata all’aumento
della finezza Blaine, ottenendo un valore finale
pari a 0.55 m2/g.
Per la cenere tal quale (PMAtq), la percentuale
di materiale passante attraverso il setaccio da
0.150 mm è pari a circa l’80% (Fig. 1). Questa
informazione è stata tenuta in considerazione in
fase di proporzionamento delle miscela di
calcestruzzo autocompattante al fine di
controllare correttamente la quantità di filler
effettivamente introdotto nella miscela stessa.
Due immagini della cenere tal quale ottenute
mediante microscopia elettronica a scansione con
due diversi ingrandimenti sono riportate in Fig.
2.
|
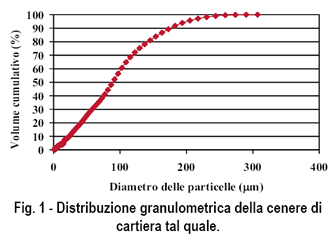
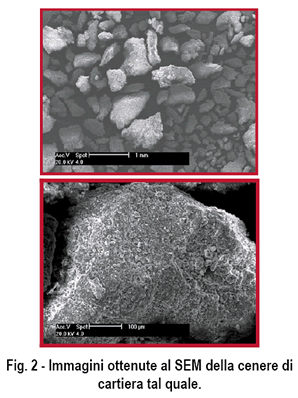
Come aggiunta minerale è stata impiegata una
polvere ottenuta come scarto della lavorazione
del marmo. La scelta è stata effettuata tenendo
presenti alcuni suggerimenti riportati in
letteratura (8), concernenti in particolare la
finezza delle polveri per calcestruzzi
autocompattanti. La finezza Blaine della polvere
di marmo era 0,61 m2/g), mentre la
sua massa volumica era pari a 2650 kg/m3;
la sua composizione chimica è riportata in
Tabella 1.
Alternativamente, come aggiunta minerale, è
stata impiegata una polvere proveniente da
processi di riciclaggio di calcestruzzo demolito.
La polvere si forma durante la fase di
macinazione del vecchio calcestruzzo, necessaria
per separarlo dall’armatura metallica e ridurlo
a pezzature idonee all’impiego come aggregato di
riciclo, ed è stata ottenuta raccogliendo il
materiale passante al setaccio con apertura
0,150 mm. La finezza Blaine della polvere di
riciclo così ottenuta era pari a 0,73 m2/g,
con una massa volumica di 2150 kg/m3;
la sua composizione chimica è riportata in
Tabella 1.
Come aggregati sono state impiegate una frazione
di sabbia naturale (diametro massimo 6 mm) ed
una frazione di ghiaietto di frantumazione (diametro
massimo 15 mm). La distribuzione granulometrica
delle due frazioni è mostrata in Figura 1 e le
principali proprietà fisiche sono riportate in
Tabella 2.
Come additivo riduttore d’acqua è stata
impiegata una soluzione acquosa al 30% di
polimero a base acrilica.
Come fibre, in alcune miscele sono state
impiegate fibre in acciaio uncinate dosate allo
0,6% in volume. Tale dosaggio è stato stabilito
sulla base di alcune informazioni riportate in
letteratura (9-11), che mostrano come un aumento
del contenuto di fibre dallo 0,5% all’1,0%
comporti un calcestruzzo complessivamente meno
preformante.
In alternativa, sono state impiegate fibre
polimeriche, sia in polivinilalcol (PVA) sia in
polipropilene ad elevata tenacità (PPHT),
aggiunte con dosaggi rispettivamente pari a 0,8
% e 0,6% in volume. La lunghezza ed il diametro
delle fibre, il valore del rapporto d’aspetto,
il modulo elastico e la resistenza a trazione
delle stesse sono riportati in Tabella 3.
Inoltre, la loro morfologia è osservabile in
Figura 2.
PROPORZIONAMENTO DELLE MISCELE
Sono state preparate quattro diverse miscele di
calcestruzzo autocompattante con lo stesso
rapporto acqua/cemento pari a 0.54, lo stesso
dosaggio del cemento (370 kg/m3) e
degli inerti ma cambiando il tipo di aggiunta
minerale (Tabella 1).
Per la miscela di riferimento (RIF) è stato
impiegato filler calcareo, il cui impiego per la
preparazione di calcestruzzi autocompattanti è
ormai consolidato, poi è stata impiegata cenere
tal quale in parziale sostituzione del filler
calcareo per la miscela (L+PMAtq) ed infine
cenere macinata in parziale o totale
sostituzione del filler calcareo per le miscele
‘L+PMAmac’ e ‘PMAmac’ rispettivamente. Quando è
stata impiegata la cenere di cartiera tal quale
(PMAtq), il controllo del dosaggio introdotto è
stato particolarmente difficile per la
variabilità dei risultati ottenuti in fase di
misurazione del suo volume apparente. È stato
adottato un valore di massa volumica apparente
pari a circa 1.2 g/cm3 per
la cenere tal quale, mentre la massa volumica
misurata per la cenere macinata è risultata pari
a 2.1 g/cm3. Il dosaggio delle
aggiunte minerali è stato scelto sulla base di
considerazioni volumetriche per raggiungere un
volume complessivo di particelle finissime nelle
miscele (incluso quindi il cemento) pari a
180-190 litri per metro cubo di calcestruzzo. In
questo modo il rapporto tra i volumi di acqua
d’impasto e materiale finissimo è risultato
compreso nell’intervallo 1.0-1.05.
Sono stati inoltre impiegati due diversi tipi di
additivi chimici: un superfluidificante a base
acrilica con un dosaggio compreso tra 1.1-1.4%
sul peso del cemento e, in alcuni casi, un
additivo modificatore di viscosità (VMA) con un
dosaggio pari allo 0.05% o 0.1% sul peso del
cemento. In presenza di cenere di cartiera
macinata, il dosaggio di additivo riduttore
d’acqua è risultato maggiore per la maggiore
richiesta d’acqua del filler caratterizzato da
una finezza più elevata. Per lo stesso motivo
non è stata necessaria l’aggiunta di additivo
VMA nel caso di impiego di cenere macinata,
infatti le miscele presentavano già un buon
comportamento coesivo.
Per quanto riguarda le frazioni di aggregato
impiegate, sabbia silicea e ghiaietto di
frantumazione sono stati proporzionati al 54% e
46% rispettivamente. In questo modo il rapporto
tra i volumi di sabbia e quello di malta è
risultato pari a 0.45 ed il volume di aggregato
grosso molto basso, pari a 265 litri per metro
cubo di calcestruzzo.
PRISULTATI E DISCUSSIONE
Prova allo stato fresco: slump flow
Il comportamento reologico del calcestruzzo allo
stato fresco è stato valutato mediante prova
dello slump flow, misurando sia il diametro
medio della focaccia di calcestruzzo sia il
tempo necessario al conseguimento della
configurazione finale. I risultati ottenuti per
le quattro miscele studiate sono riportati in
Tabella 2.
Tutte le miscele hanno mostrato una adeguata
deformabilità sotto l’azione del peso proprio.
Infatti il valore del diametro medio della
focaccia è sempre risultato superiore a 600 mm,
a parte il caso in cui è stata impiegata cenere
tal quale, per cui il valore misurato è stato di
580 mm. Anche in termini di viscosità (valutabile
mediante la misura dei secondi intercorsi prima
dell’arresto), tutte le miscele hanno mostrato
un buon comportamento ad eccezione della miscela
di riferimento che è sembrata troppo viscosa. Il
motivo di tale eccesso di viscosità è
probabilmente ascrivibile all’elevato dosaggio
di VMA impiegato (0.1% in peso sul cemento).
Comunque in nessun caso sono stati notati
fenomeni di segregazione quali la comparsa di
un’aureola di pasta cementizia attorno alla
focaccia di calcestruzzo o il cosiddetto effetto
sombrero.
Prove allo stato indurito: resistenza a
compressione
La resistenza a compressione dei calcestruzzi
autocompattanti è stata misurata su provini
cubici (100x100x100 mm) a tempi di stagionatura
crescenti: 1, 3, 7, 14 e 28 giorni. Tutti i
provini, dopo lo scassero avvenuto a 24 ore dal
getto, sono stati mantenuti in condizioni di
umidità relativa pari ad almeno il 95%, ad una
temperatura di 20°C.
I risultati ottenuti sono riportati in Tabella 3
e mostrati graficamente in Fig. 3. Si può notare
come la cenere di cartiera tal quale abbia
leggermente penalizzato le prestazioni
meccaniche del calcestruzzo (-4%). Una possibile
spiegazione a cui si potrebbe imputare tale
comportamento risiede nell’indebolimento della
matrice cementizia conseguente alla elevata
porosità della cenere tal quale. Al contrario,
l’impiego di cenere di cartiera macinata
caratterizzata da un elevato valore di finezza,
leggermente superiore a quello del filler
calcareo di riferimento, ha consentito il
raggiungimento di un’ottima prestazione
meccanica particolarmente alle medie e lunghe
stagionature (+30% in caso di totale
sostituzione del filler calcareo). Tale aumento
della resistenza a compressione può essere
imputabile alla maggiore finezza della cenere di
cartiera macinata e quindi ad un maggiore
effetto fillerizzante della stessa. Benché tale
cenere contenga ossidi di alluminio e silicio,
sembrerebbe azzardato ipotizzare un’eventuale
attività pozzolanica attivata dall’azione della
macinatura con conseguente aumento della
superficie specifica delle particelle di cenere
Prove allo stato indurito: misure di ritiro
igrometrico
Il comportamento deformativo alle lunghe
stagionature dei calcestruzzi autocompattanti
sottoposti ad essiccamento è stato valutato
mediante prove di ritiro igrometrico su provini
prismatici (100x100x500 mm) a partire da 1
giorno dal getto fino a sei mesi. I provini dopo
lo scassero sono stati esposti ad un ambiente
condizionato con umidità relativa del 60% e
temperatura di 20°C. I risultati ottenuti sono
riportati in Fig. 4.
Rispetto alla miscela di riferimento l’impiego
di cenere di cartiera in qualsiasi modalità (tal
quale o macinata) ha prodotto valori di ritiro
leggermente superiori. In particolare, nel caso
di cenere tal quale è stato rilevato un valore
del ritiro igrometrico dopo 180 giorni superiore
del 12% rispetto alla miscela di riferimento. Il
motivo in questo caso potrebbe essere
ascrivibile al volume maggiore di materiale
finissimo e/o alla maggiore porosità della
miscela ‘PMAtq’ rispetto alla miscela ‘RIF’.
Nel caso di impiego della cenere macinata, il
valore del ritiro igrometrico dopo 180 giorni è
risultato superiore a quello della miscela di
riferimento del 16% o 30% a seconda della
percentuale di sostituzione (il valore più
elevato di ritiro corrisponde ad una
sostituzione del 100%). In questo caso la
maggiore sensibilità all’essiccamento del
calcestruzzo può essere imputabile alla maggiore
finezza dell’aggiunta minerale impiegata con
conseguente aumento dell’acqua assorbita dalla
stessa.
CONCLUSIONI
Sulla base dei risultati sperimentali ottenuti
in questa sperimentazione si possono trarre le
seguenti conclusioni di carattere generale:
● l’impiego di cenere di cartiera tal quale
sembrerebbe promettente in termini di
comportamento reologico allo stato fresco in
presenza di additivo modificatore di viscosità;
● tuttavia, quando viene impiegata cenere di
cartiera tal quale le prestazioni meccaniche del
calcestruzzo autocompattante ed il ritiro
igrometrico risultano leggermente penalizzati
rispetto ai risultati ottenuti per la miscela di
riferimento;
● l’impiego di cenere di cartiera macinata è
sembrato vantaggioso in termini di miglioramento
del comportamento reologico allo stato fresco
del calcestruzzo autocompattante, anche in
assenza di additivi modificatori di viscosità;
● quando la cenere di cartiera macinata è stata
impiegata al 100% ha comportato un significativo
miglioramento delle prestazioni meccaniche del
calcestruzzo (+30%) principalmente per un
migliore effetto fillerizzante rispetto al
filler calcareo;
● d’altra parte, quando è stata impiegata cenere
di cartiera macinata in totale sostituzione del
filler calcareo è stato rilevato un incremento
significativo del ritiro igrometrico dopo sei
mesi, imputabile alla maggior finezza
dell’aggiunta minerale impiegata.
RIFERIMENTI
Asquini, L., Furlani, E., Bruckner, S., Maschio,
S. (2008). “Production and characterization of
sintered ceramics from paper mill sludge and
glass cullet.”, Chemosphere, 71, 83–89.
Bonen, D., and Shah, S.P. (2005). “Fresh and
hardened properties of self-consolidating
concrete”, Progress in Structural Engineering
and Materials, 7(1), 14-26.
Borsoi, A., Collepardi, M., Collepardi, S.,
Croce, E.N., Passuelo, A. (2006) “Influence of
Viscosity Modifying Admixture on the Composition
of SCC” Proceedings of Eight CANMET/ACI
International Conference on Superplasticizers
and Other Chemical Admixtures in Concrete,
Supplementary Papers, 2006, 253-261.
Collepardi, M., Borsoi, A., Collepardi, S.,
Troli, R. (2005). “Strength, Shrinkage and Creep
of SCC and Flowing Concrete” Proceedings of
Fourth International RILEM Symposium on
Self-Compacting Concrete, Ed. By S.P. Shah,
Chicago, MI, USA, vol. 2, 911-919.
EN 197-1. “Cement – Part 1: Composition,
specifications and conformity criteria for
common cements.” CEN, 2000.
Ernstbrunner, L. (1997). “Rejects from paper
manufacture utilized in the cement works”,
Papier 51 (6), 284–286.
Khayat, K.H., Guizani, Z. (1997). “Use of
viscosity-modifying admixture to enhance
stability of fluid concrete”, ACI Materials
Journal, 94(4), 332-340.
Liaw, C.T., Chang, H.L., Hsu, W.C., Huang, C.R.
(1998). “A novel method to reuse paper sludge
and cogeneration ashes from paper mill.”, J.
Hazard. Mater. 58, 93–103.
Marcis, C., Minichelli, D., Bruckner, S.,
Bachiorrini, A., Maschio, S. (2005). “Production
of monolithic ceramics from incinerated
municipal sewage sludge, paper mill sludge and
steelworks slag”, Ind. Ceram. 25 (2), 89–95.
Okamura, H., and Ozawa, K. (2003). “Mix design
for Self-Compacting Concrete”, Concrete Library
of JSCE, Rejkjavik, Iceland, 107-120.
Troli, R., Ogoumah Olagot, J.J., Monosi, S.,
Collepardi, M. (2003) “Low Heat Development in
Self-Compacting Concrete for Massive Structure”,
Proceedings of Seventh CANMET/ACI International
Conference on Superplasticizers and Other
Chemical Admixtures in Concrete. ACI SP 217-10,
103-112.
|